How on-time delivery and quality obsession in fabrication save you time and money. |
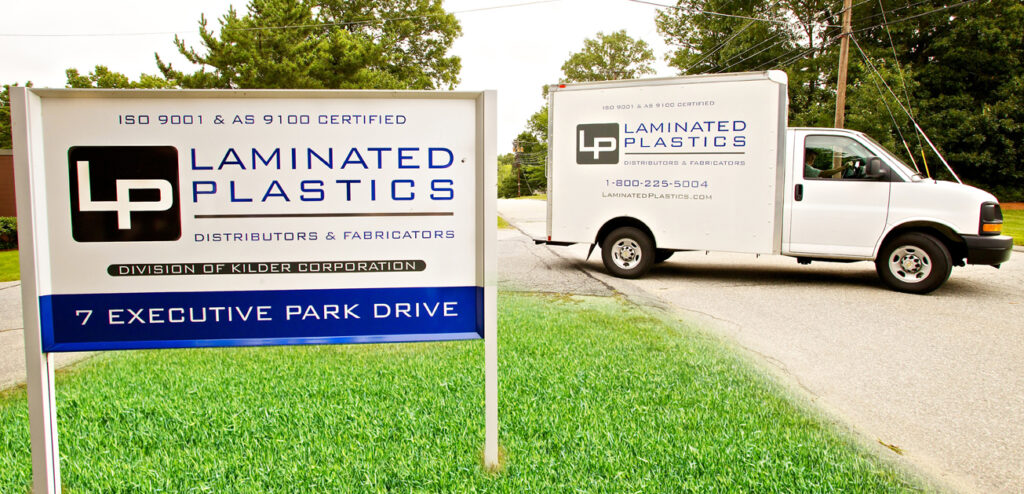
In the military, there’s a phrase that captures the balance of speed and precision: “smooth is fast, fast is smooth.” This principle resonates deeply within the realm of plastics fabrication. While many companies offer fabrication services, few consistently deliver the delicate balance of speed and precision that keeps projects moving forward efficiently while ensuring exactness in dimensions, machining, and production.
A critical component of “fast”—or, more accurately, on-time delivery—is ensuring that every detail is captured correctly from the outset. From the quoting process to the First Article Inspection (FAI), fabricators must focus on details like dimensions, tolerances, material specifications, and certification requirements. Accurately gathering and understanding this information before production begins is essential to maintaining a “smooth” operation throughout.
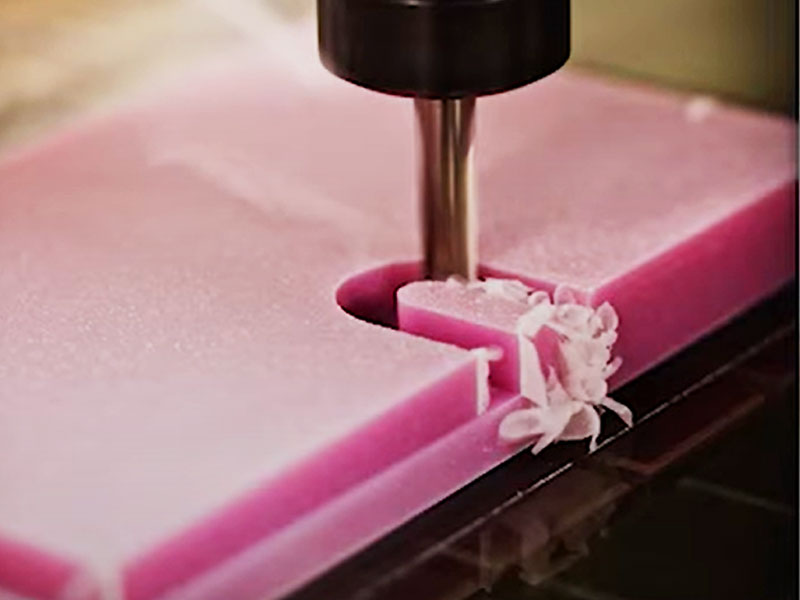
Once setup is complete and all details are addressed, production can begin. To ensure consistent quality, machine operators conduct spot checks during production, verifying that parts remain within tolerances and that all required machining is completed prior to final inspection. This layered approach allows us to identify and address potential issues before they become costly errors.
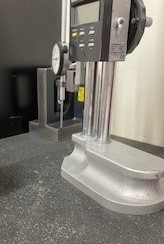
Final inspection is where precision meets customer expectations. Here, inspectors rigorously review parts against the purchase order and drawing requirements, ensuring that everything aligns perfectly. This thorough process significantly reduces the risk of errors, ultimately supporting both accuracy and on-time delivery.
While human error is inevitable, adhering to a rigorous and consistent process from quoting to final inspection dramatically reduces the chances of delays and defects. At Laminated Plastics, our commitment to this process helps us ensure on-time delivery and high-quality parts for our customers.